In less than 100 days, the 44th edition of the famous Dakar Rally will kick off. For Audi Sport, this marks the beginning of a real race against time.
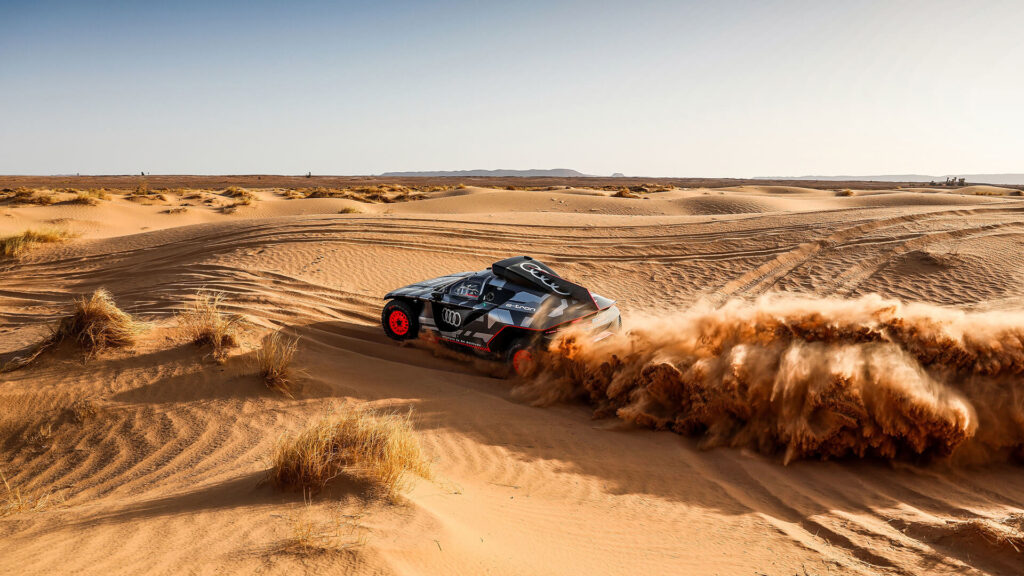
Audi is tackling one of the greatest challenges in international motorsport, quite deliberately using a unique
concept. The Audi RS Q e-tron has an electric powertrain with two motor-generator units (MGUs) from Formula
E. While the vehicle is in motion, the high-voltage battery is charged by an energy converter consisting of the
efficient TFSI engine from the DTM and another MGU.
“The prototype of the Audi RS Q e-tron was created in around twelve months,” says Julius Seebach, Managing
Director of Audi Sport GmbH and responsible for motorsport at Audi. The rollout on June 30th, 2021 in
Neuburg an der Donau and the start on January 1, 2022 in Ha’il (Saudi Arabia) are separated by merely six
months. “That’s a very short time to prepare for such a complex project. I cannot emphasise this often enough:
The Audi RS Q-etron is the most sophisticated vehicle in terms of technology that Audi Sport has ever deployed
in racing.”
Andreas Roos, Project Leader for all factory-backed motorsport activities, can only confirm that: “The Dakar is
extremely challenging – even for a conventionally powered vehicle. With our powertrain concept, the challenge
is distinctly greater. The chassis and suspension do not entail major differences, but we have a lot more
components in the car that have to be not only high performing lightweight and functioning reliably under the
extreme conditions of the Dakar. They also have to be attuned to each other perfectly and work together
smoothly.”
A conventionally powered Dakar vehicle features two major components: the internal combustion engine and the
transmission. “In our Audi RS Q e-tron, we have an electric motor at the front axle, an electric motor at the rear
axle, the high-voltage battery and the energy converter, consisting of another MGU and the TFSI engine from
the DTM,” says Roos. “And each of these components, for instance, requires a dedicated cooling system. That
means we have not only one cooling system in the car but as many as six, including the intercooler and air
conditioning system for the driver and co-driver.”
Packaging is another major issue with such a complex vehicle. “We had to make use of every centimetre to
accommodate all the components in the car,” says Roos. That comes at the cost of ease of service. “For instance,
changing the front-axle differential still takes a lot of time at the moment. That must be achievable faster at the
Dakar and is one of the issues we’re currently working on under massive time pressure.”